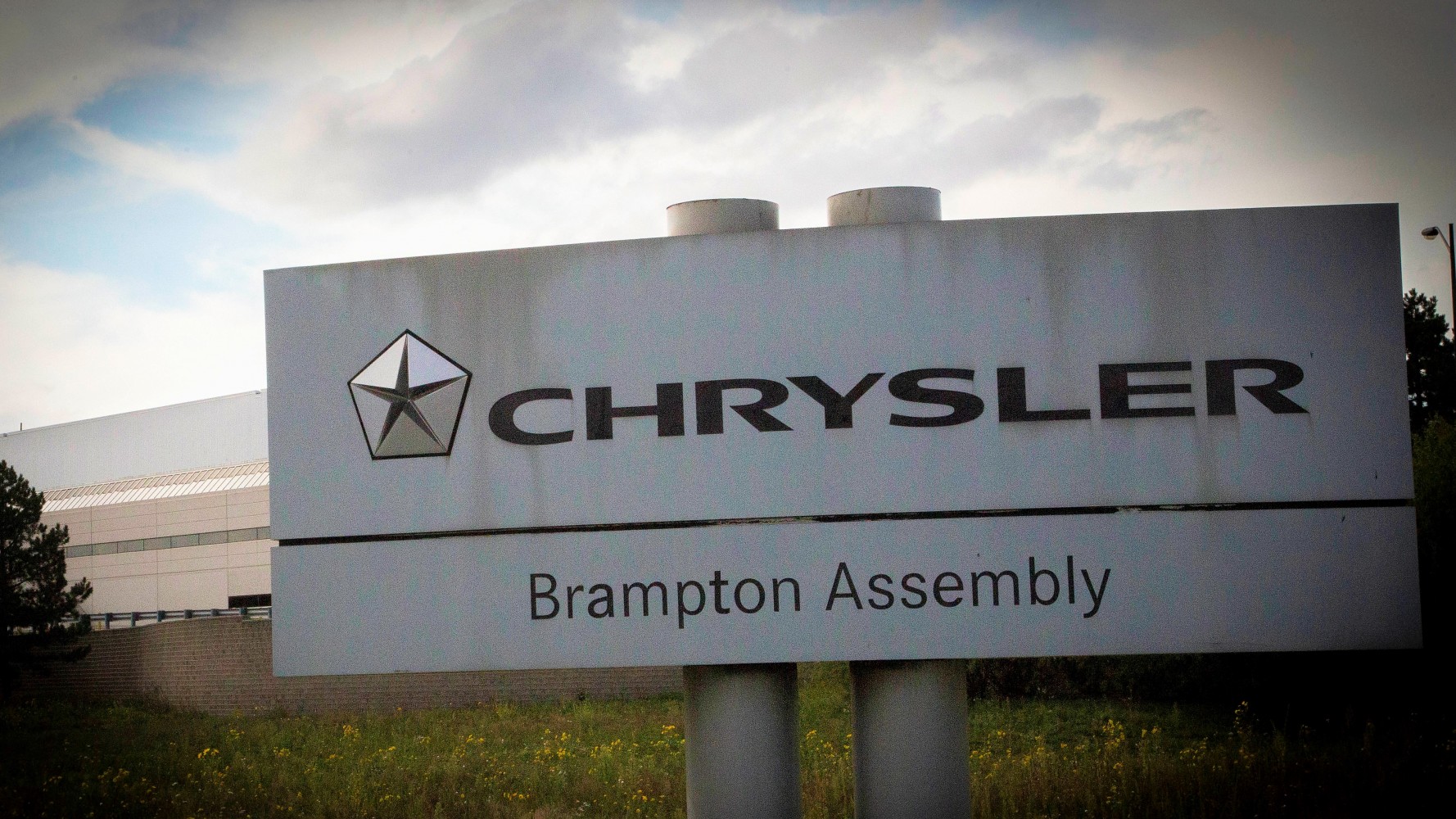
Oshawa’s worst nightmare is a wake-up call for Brampton
Leon Rideout is quietly concerned. The ex-president of Unifor Local 1258 at the Fiat Chrysler plant on Williams Parkway has a few minutes before he has to catch Jerry Dias on TV. The president of Unifor’s national office is speaking at a press conference about Oshawa — ground zero this week for the labour movement in Ontario.
General Motors has just issued a statement saying it is closing its Oshawa facility as it moves toward building the products of the future — electric and self-driving cars. This continues a pattern away from the production of gas-powered sedans, which are losing market share by the minute to SUVs, crossovers, hybrids and electric vehicles. GM’s move will put 2,500 out of work in Oshawa and shutter four other plants in the U.S. The company is also shedding 15 percent of its white-collar work force, a coordinated decision that will save one of the world’s largest automakers $6 billion by 2020.
The company didn’t answer questions about how much its leaving will cost this community just east of Toronto. It’s probably hard to say, considering the domino effect and the potential magnitude of the loss.
The announcement gives Rideout pause for two reasons: he knows it will fill his former colleagues at the Brampton plant with anxiety; and because the facility is driven by two lines of sedans, the Dodge Charger and Dodge Challenger.
Sales of the Charger in the U.S., for example, have been sinking recently, from about 97,000 in 2016 to a 2018 pace projected to finish at around 80,000 sales by the end of the year. That’s close to an 18 percent decline in two years, and global sales figures for the two models already represent much lower numbers compared to the best selling sedans in the world. In just the first six months of this year, Toyota’s Camry registered almost 179,000 sales in America.
If this sudden closure can happen at one of GM’s biggest and oldest plants, in the city dubbed “Canada’s Automotive Capital,” it can happen in Brampton, too. It’s time for local leaders to start looking at other examples, including Janesville, Wisc., a car-making town rebuilding after a plant shutdown devastated its economy.
Of Fiat Chrysler’s 159 global manufacturing facilities, including assembly plants in countries where wages are much lower, Brampton’s is one of the oldest and it’s making two muscle cars that fill a shrinking niche market. With the trend toward new types of vehicles, in an investor climate that no longer allows the sort of status quo thinking that in the past got the company in trouble for failing to innovate and find efficiencies, the viability of its local operation could be questioned.
The Dodge Charger made in Brampton
Rideout says the approximately 4,000 people he once worked with on Williams Parkway “must be looking over their shoulder.” Or maybe into their rearview mirrors.
Just a few months ago, as negotiations with American negotiators over a deal to replace NAFTA dragged on, U.S. President Donald Trump threatened to impose a 25 percent tariff on cars built here — a call that sent a shiver through the $50-billion auto industry in Canada.
A deal (dubbed USMCA, the United States Mexico Canada Agreement) was finally struck, and workers at the Brampton plant let out a collective sigh. “There was so much at stake for all of us,” said Jaspal Brar, an assembly line installer and the retired Rideout’s replacement as president of the local.
The Big Three automakers that dominated the post-war manufacturing boom in North America — Ford, GM and Chrysler – were once safe landing pads for workers looking to score a “job for life.”
That safety net is now gone. Canada is still a competitive country in the auto business because of its low dollar and well-trained workforce, but cars can be built cheaper south of the border, and cheaper still in Mexico and stupidly cheap in other parts of the world. Retaining competitive balance has become a game of Jenga.
It was only a decade ago that the domestic auto industry was choking on fumes. The only thing that saved the Big Three from the economic meltdown of 2008 was vast infusions of cash from Washington and Ottawa.
Rideout remembers when the Chrysler plant in Brampton was teetering on the brink. “These were very anxious times when the future of the industry [and our plant] was iffy,” he says.
If Rideout frets quietly for his former union members today, Dias was loud and angry. At his presser on Monday, he said, “They [GM] are not closing our damn plant without a hell of a fight.”
Global News reported that he compared GM leaving Oshawa — after getting billions in combined federal and provincial bailout dollars after 2008 — as tantamount to giving Canadian workers “the middle finger.” And so, said Dias, Ottawa needs to give it right back to the automaker.
Rideout says GM has a history “of doing this kind of stuff” and points to its initiative a few years back to close an Oshawa truck plant, even though it was the number one producer in the industry.
While auto workers were dismayed by Monday’s announcement, stock pickers were downright giddy. GM rose 5 percent in value in the markets, and industry experts see a company reinventing its line of products to prepare for the changing wants of fickle consumers. And a planet desperately in need of clean air.
Which begs the question: if the best stock pickers are those who diversify their portfolio, why don’t cities like Oshawa break their dependence on one industry sector?
Oshawa MP Jennifer French issued a statement after the announcement, saying GM is turning its back on 100 years of history in Canada and abandoning not only the Oshawa workers but their families.
Premier Doug Ford, in a rare moment of clarity, and realism, has advised that there is nothing else the province can do. GM, a public company that answers to shareholders, has made its decision.
Talk is now shifting to a possible intervention by the federal government. Eventually, reality will set in.
Word of the pending closure had begun swirling Sunday night, blindsiding workers and civic officials alike, according to Mayor John Henry, who was born in Oshawa to an auto-worker father. He said he had no inkling the move was coming.
Cities like Oshawa, or Brampton, need to be ready when one of their major manufacturers is threatened with closure. The impact to the city can be devastating — especially for hundreds of employees and their families. And what about the ancillary businesses directly impacted by a shutdown — everything from small auto-parts makers to local restaurants and convenience stores feeding off the company, or its employees?
It’s odd that Oshawa’s mayor and council were so caught off-guard by an announcement other experts saw coming. Joe McCabe, CEO of AutoForecast Solutions LLC, predicted the 2019 closure four years ago. He said the warning signs were everywhere, especially in the two lines of low-volume cars the plant was producing: the Cadillac XTS and Chevrolet Impala. This wasn’t based “on NAFTA 2.0 or anything else of that nature,” he added.
Oshawa’s dilemma is a warning sign to Brampton that one of its largest manufacturing facilities is vulnerable to the unpredictability of the ever-changing automobile market.
Thirty-two years ago, American Motors expanded to a 269-acre site on Williams Parkway. The 2.95-million-square-foot facility was immense, and everything was built under one roof — except for its satellite stamping plant. With over 32 km of conveyors and more than 500 robots, this was a modern-day marvel of engineering and production. The assembly lines have produced many vehicles over the years, but today, the plant is home to the Hellcat-engineered Challenger and Charger.
What would happen if Fiat Chrysler announced its Brampton plant wasn’t part of its larger global restructuring plans, as GM told its Oshawa audience?
That’s why the news Monday was both powerful and symbolic. It’s what keeps Rideout and Brar in a constant state of unease.
Rideout worked for both AMC and Chrysler. He worked in Brampton in the 1970s and ‘80s, the halcyon years for manufacturing. Jobs were high-paying and many went a-begging because there weren’t enough workers to fill them. “Manufacturing was just so huge back then,” he says. “There were wallpaper factories, and some that made steering wheels, and others that built carburetors. Now you look around, and all you see are warehouses.”
Rideout’s description of Brampton as a hub for busy shop floors and workers who were paid good wages actually extended into the ’90s. Firms like Nortel, Caterpillar, Benson & Hedges and American Motors were in their ascendency, and one resident remembers Brampton in that era as a city of “work boots and hockey jackets.”
But the manufacturing boom sputtered out with the demise of its largest employer. Nortel Networks rode the telecom boom of the late 1990s and early 2000s and became the 12th largest company in the world, employing over 50,000 worldwide, including 5,000 at its manufacturing facility on Dixie Road in Brampton. Then it increased its debt load, expanded too quickly, and when the dot.com boom went bust, so did company’s fortunes. Its stock price toppled from $126 to penny stock status. Market capitalization declined from $398 billion to less than $5 billion, and its 50,000 workers (including the 5,000 here) lost everything, including their rich pension plans — leading to a long, drawn-out battle for justice in the courts that was only settled (in the workers’ favour) last year. Caterpillar exited the city in 1991 and left 400 looking for work. Benson & Hedges collapsed as societal norms changed and the cigarette industry collapsed on itself. American Motors lost customer share, and in the early 1990s its giant facility at Kennedy and Steeles was plowed under where a Walmart now stands. At least it was bought out by Chrysler, which soon replaced Nortel as the city’s largest employer.
There are still remnants of the manufacturing industry scattered throughout the city today. Earlier this year, an era ended when Dixie Cup closed its doors and put 133 workers on the streets. It had been a Brampton mainstay for 69 years.
Dixie Cup’s closing was duly noted by Patrick Brown as he ran for mayor this past summer and fall. Its closing was, he said, symbolic of the lack of economic opportunities for residents of this city. In The Pointer’s debate held at Sheridan College, he said it was sad that more than 60 percent of residents have to leave the city every day to go to work, and he vowed to bring new business — especially manufacturing — back to Brampton through incentives and dogged selling. He pointed to the growing imbalance in residential-to-employment lands here and said, “there’s no excuse for it. Look, even now we have an empty building at Dixie Cup. I want the opportunity to market Brampton.”
He eventually got that opportunity, a chance to make good on his stated determination to find new employers and jobs for about 115,000 people over the next decade.
Janesville, Wisc., (located between Chicago and Madison) offers the kind of tragic but uplifting story that all employees in the auto manufacturing business should read. Janesville: An American Story was written by Pulitzer Prize–winning reporter Amy Goldstein of the Washington Post. It’s a tale about GM’s oldest plant (opened in 1923) being felled by the economic disaster of 2008, with everything closed by 2015. Goldstein called the 4.8-million-square-foot plant at the south end of the city the “grand cathedral of industry.” The author talked to its workers, educators, bankers, politicians, and job re-trainers, writing that when something is lost (thousands of jobs), something can be found (self-worth, and a city’s soul). It’s a cautionary tale about a city watching its biggest employer crash and burn — and almost take the town itself with it.
By 2008, GM had acquired a worldwide debt load of $172.8 billion, and when the economy tanked, workers were left naked and alone. Most stayed that way, even when Washington and Ottawa deemed the company too big to fail.
Goldstein says a city’s very rhythms are tied to its major industry (traffic flow, train schedules, work schedules, shift changes, restaurant openings, school celebrations, etc.), and breaking that rhythm is traumatic. But the book is a stirring tale of resilience and renewal, for the GM workers and the city itself. One book reviewer asked a simple question: Why hadn’t the city prepared earlier for the possibility that one day a major business might fail?
It’s a question Oshawa now has to answer.
It’s something Brampton should be preparing for.
GM leaving is a body-blow to Oshawa. It has thrown the city off-rhythm. But, unlike Brampton, Oshawa has already done some prep work for its future. It’s home to three postsecondary institutions (Durham College, the University of Ontario Institute of Technology and a campus of Trent University) and has a strong foothold in the healthcare field. In 2016, it was the sixth-best place in Canada to find full-time employment, based on data from StatsCan.
Is Brampton as diversified?
Is the possible shutdown of a major industry part of future planning?
Brown needs to educate himself on Brampton’s business strengths, and most importantly, its weaknesses. The city can’t afford to be taken by surprise if and when one of its major employers closes down. Like good stock pickers, cities have to diversify their portfolios. Overloading in one sector creates a vulnerability, another Janesville.
Rideout remembers the angst surrounding the 2008 bankruptcy and the eventual partnership between Chrysler and Fiat. The union made major concessions so the new-look company could survive and thrive. But the company also made a commitment to its work force and city. Rideout remembers when he and Dias travelled to both Chrysler’s headquarters in Detroit and Fiat’s in Italy to see the firm’s new operations system and learn about its future plans.
The move to “smart manufacturing” would pay off over the years. So far, so good: the plant runs two shifts, five days a week.
During the last negotiations, millions were poured into plant upgrades, and there’s hope of a new production plan post-2020.
But there are worries. Sedan sales could continue to tank. Gas prices might rise again, making it a challenge to buy muscle cars like the Challenger.
Rideout, who still follows the industry as closely as anyone, sees good news for his old plant in the fact that Ford recently announced it is discontinuing most of its sedan production, including the Taurus. It’s one of the cars purchased by police forces across North America. The other is the Dodge Charger, built right here.
He hopes fleet sales of Chargers will guarantee the plant’s future. But in the auto industry, there are no guarantees. It’s 2018, not 1974. Markets change. Tastes vary. Even police forces are eyeing SUVs and crossovers.
Rideout is realistic about the future of manufacturing. He says workers have to continually upgrade their skills, and luckily this city’s Sheridan College campus offers one of the best training facilities anywhere, its Centre for Advanced Manufacturing.
Bad economic news in the past has eaten away at the confidence of workers who once hoped for a “job for life.”
Employees at the Williams Parkway plant once had to wait only 18 months before receiving full wages and benefits. That “grow-in period” now stretches to 10 years.
The question they have to ask themselves now isn’t whether they’ll make it to full pay status, but whether their company will be there at all a few years from now.
GM’s announcement on Monday was their slap in the face.
Submit a correction about this story